What Are the Best Practices for Safe Maintenance
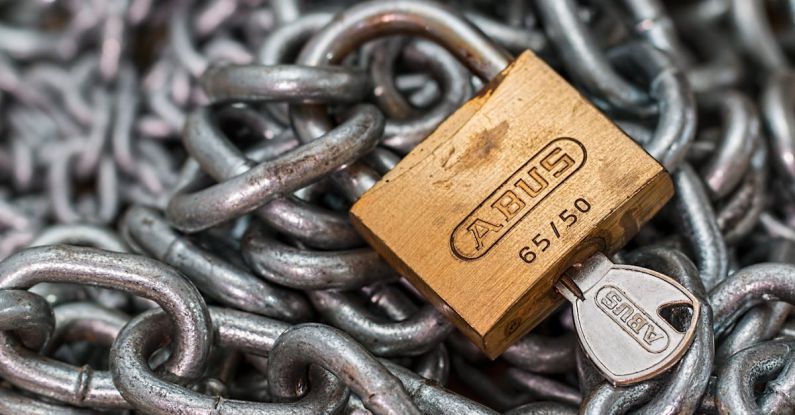
Ensuring Safe Maintenance Practices in the Workplace
Maintenance work is an essential aspect of keeping equipment, machinery, and facilities in optimal condition. However, it also poses various risks to the maintenance personnel involved. To mitigate these risks and promote a safe working environment, it is crucial to adhere to best practices for safe maintenance. By implementing proper safety protocols, organizations can prevent accidents, injuries, and costly downtime. In this article, we will explore the key practices that can help enhance safety during maintenance activities.
Establishing a Comprehensive Safety Program
A fundamental aspect of ensuring safe maintenance practices is the development and implementation of a comprehensive safety program. This program should outline the specific safety procedures and protocols that need to be followed during maintenance work. It should also include guidelines for hazard identification, risk assessment, and the use of personal protective equipment (PPE). By establishing a clear safety program, organizations can ensure that all maintenance personnel are aware of the potential risks involved and the necessary precautions to take.
Conducting Regular Safety Training
Another crucial practice for safe maintenance is providing regular safety training to maintenance personnel. This training should cover a range of topics, including hazard awareness, safe work practices, emergency procedures, and the proper use of equipment and tools. By ensuring that maintenance workers are well-trained in safety protocols, organizations can reduce the likelihood of accidents and injuries. Regular safety training also helps to reinforce the importance of safety in the workplace and promotes a culture of safety among maintenance staff.
Implementing Lockout/Tagout Procedures
Lockout/tagout procedures are essential for ensuring the safety of maintenance personnel when working on equipment or machinery. These procedures involve isolating energy sources and securing them with locks or tags to prevent accidental startup during maintenance activities. By implementing lockout/tagout procedures, organizations can protect maintenance workers from serious injuries caused by unexpected energy release. It is crucial to train maintenance personnel on proper lockout/tagout procedures and ensure that these protocols are consistently followed.
Conducting Risk Assessments
Prior to conducting any maintenance work, organizations should conduct thorough risk assessments to identify potential hazards and develop appropriate control measures. Risk assessments help in determining the level of risk associated with specific maintenance tasks and enable organizations to implement preventive measures to mitigate these risks. By identifying and addressing potential hazards proactively, organizations can prevent accidents and injuries during maintenance activities.
Maintaining Equipment and Tools
Regular maintenance of equipment and tools is essential for ensuring the safety of maintenance personnel. Faulty or poorly maintained equipment can pose significant risks to workers during maintenance work. Organizations should establish a robust maintenance schedule for equipment and tools, including inspections, repairs, and replacements as needed. By ensuring that equipment is in good working condition, organizations can minimize the risk of accidents and injuries resulting from equipment failure.
Promoting a Safety Culture
Creating a safety-conscious culture within the organization is vital for ensuring safe maintenance practices. This involves fostering a work environment where safety is prioritized, and all employees are encouraged to actively participate in maintaining a safe workplace. Organizations should promote open communication about safety concerns, encourage reporting of hazards, and recognize and reward safety-conscious behavior. By promoting a safety culture, organizations can create a positive and proactive approach to safety that helps prevent accidents and injuries during maintenance activities.
Conclusion: Emphasizing Safety in Maintenance Activities
In conclusion, implementing best practices for safe maintenance is crucial for protecting the well-being of maintenance personnel and promoting a safe working environment. By establishing a comprehensive safety program, providing regular safety training, implementing lockout/tagout procedures, conducting risk assessments, maintaining equipment and tools, and promoting a safety culture, organizations can enhance safety during maintenance activities. Prioritizing safety in maintenance work not only minimizes the risk of accidents and injuries but also contributes to increased efficiency, productivity, and overall workplace well-being. By following these best practices, organizations can create a safer and more secure environment for maintenance personnel to carry out their responsibilities effectively.